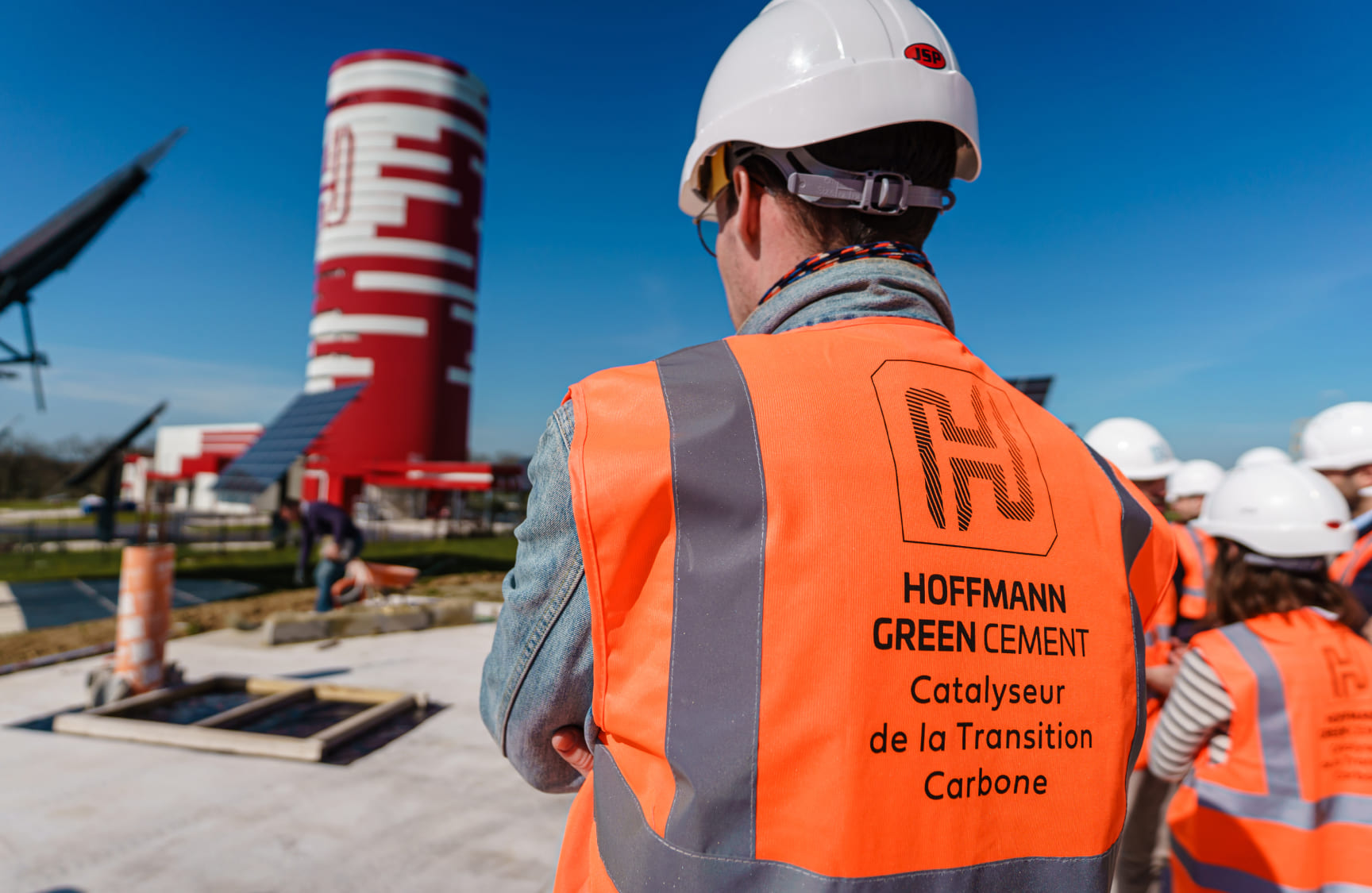
The French cement industry has pledged to reduce its carbon footprint by 80% by 2050. Among the levers that can be activated: replacing fossil fuels with co-products, reducing clinker (a component of cement) in favor of other cementitious compounds, or production of new-generation cements.
The facts: France’s cement industry has a significant carbon footprint
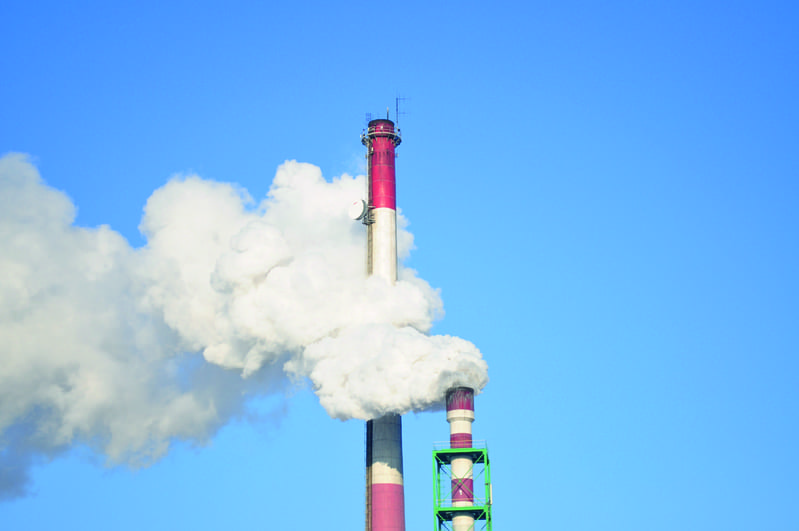
According to the International Energy Agency, the cement industry is responsible for 5-7% of C02 emissions worldwide.
The cement industry in France produces over 18 million tonnes of cement per year. It alone accounts for 2.9% of national CO2 emissions. That’s why it’s vital to innovate in the cement sector to reduce this carbon footprint.
Hoffmann Green, an innovative cement manufacturer leveraging disruptive technologies
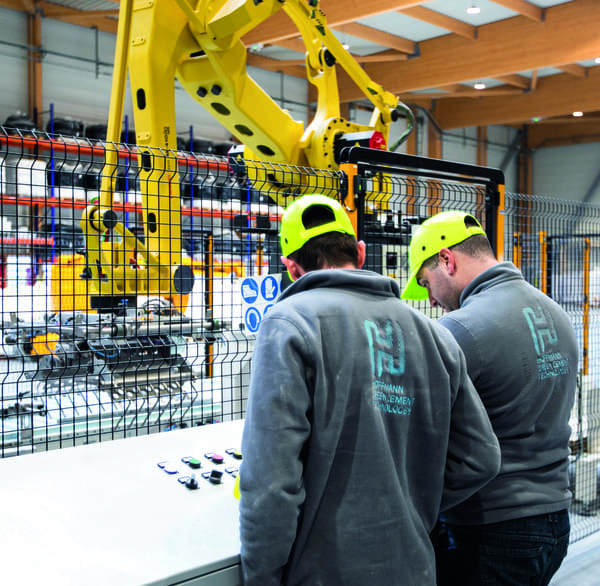
Hoffmann Green cements are based on new technologies with no firing, combustion or clinker.
As a result, these cements emit very little CO2. Hoffmann Green is referred to as low-carbon cement or decarbonated cement. Thanks to this innovation, the carbon footprint is divided by up to 5! Hoffmann Green is already surpassing the industry’s 2050 target in 2019!
Its 3 innovative cements (H-P2A, H-UKR and H-EVA) are based on alkali-activated materials and geopolymers.
This type of process makes it possible to use available co-products such as clay slurry, gypsum and slag, by mixing them with a patented matrix.
Inaugurated in November 2018, the 4.0 production unit in Bournezeau (Vendée) produces 50,000 tonnes of low-carbon cement annually for construction and prefabrication companies.
The result? Their carbon footprint is around 5 times lower than that of traditional Portland cements!